3 Modern Challenges of Manufacturing with the Composable Enterprise

Unprecedented times teach unprecedented lessons. And the last few years have taught manufacturers that even when the world around them changes in ways they never could have imagined—entire workforces trapped at home, global supply chains tied in knots, government regulations proliferating in response to each new crisis—they can still thrive if they learn those lessons well.
Mendix has been learning as well. We’ve been continuously studying how our low-code application development platform can help manufacturers quickly and affordably implement the lessons they’ve learned. One of those lessons that low-code is enabling manufacturers to put into action is that adopting the qualities of a composable enterprise can enhance an organization’s agility, increase its productivity, make it less vulnerable to disruption, and speed up its ability to innovate.
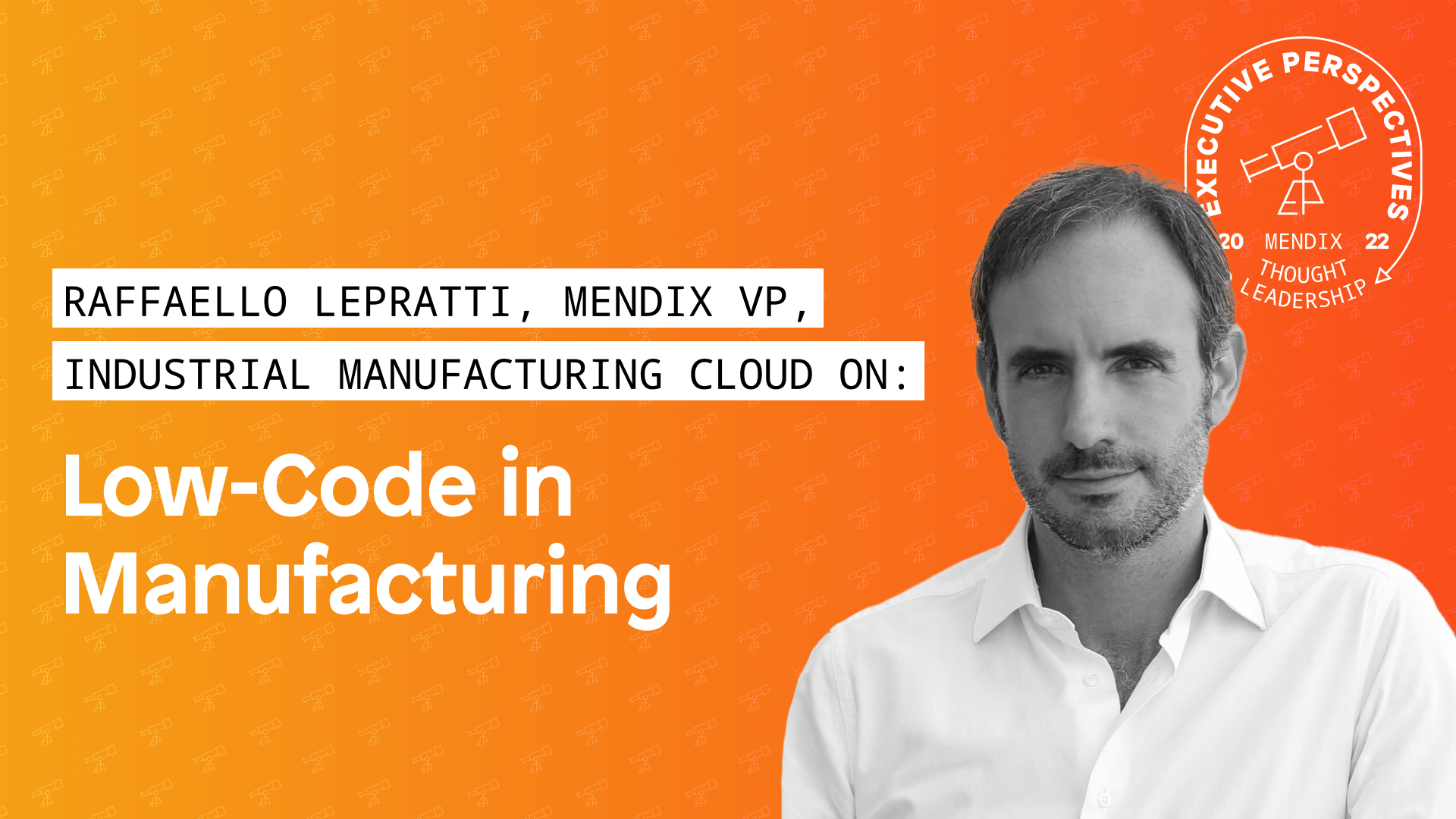
The Building Blocks of Resilience
Gartner coined the term “composable enterprise” to describe an organization architected “for real-time adaptability and resilience in the face of uncertainty.” The method that a composable enterprise uses to achieve this adaptability and resilience is by building its applications from simple, interchangeable building blocks. These building blocks can be created, updated, and shared across an organization. They can be easily tailored to support the specific requirements of the full range of domain-specific tasks across the enterprise. They also open up to a broader range of workers access to complex tools and applications that normally would be reserved for specially skilled users.
Manufacturing leaders are facing three challenges that have spurred them to take a closer look at the concepts of the composable enterprise and draw up plans for incorporating them.
1. Accommodating the demands of the marketplace
The first challenge is far from a new one. The fundamental business mission of a manufacturer has always been to get to market quickest with the highest quality product for the most affordable, while still profitable, price. But what is new is the heightened demands from the market as to what qualifies as quick, what qualifies as quality, and what qualifies as affordable.
Decades of increasing globalization have flooded the manufacturing market with competitors, all fiercely vying with each other to streamline every process, shave every cost, and push the advantage of every innovation. The pressure to meet these marketplace demands has never been higher and only continues to mount.
2. Contending with regulations
The second challenge is contending with a sprawling regulatory regime. The desperate push from governments in every corner of the world to slow, if not stop, climate change and environmental degradation have led to a patchwork of local and international regulations. And these environmental strictures are only added to those put in place to combat terrorism, slow nuclear proliferation, protect consumers, and numerous other governmental interests.
The resources manufacturers need to expend in understanding and complying with these regulations are only exceeded by the financial penalties a company faces if failing to do so. At every strategic decision branch, manufacturing leaders must ask themselves, “What are the regulatory obligations that come with building a product with this material? From this supplier? In this country? For this customer? And what are the repercussions if I misunderstand those obligations or fail to meet them?”
3. Adapting to the remote workforce
The third challenge for manufacturers is reshaping their systems to fit the realities of the remote workforce. A new way of working requires a new way of managing teams, a new way of running a shop floor, and a new way of planning production.
But what a remote workforce mostly requires from manufacturers is keeping everyone connected. That requires being able to share data readily, being able to store it securely, and being able to trust in the cloud technology you’re using to do so.
Filling the software gap
The demand for software to help manufacturers meet these challenges is skyrocketing. But the traditional way of delivering software has not been able to keep step with the demand. This gap between demand and delivery constrains manufacturers’ ability to execute their plans for digitalization and risks diluting their competitiveness. Filling that gap is where composability, and the low-code application development technologies that support composability, come into play.
The composable enterprise is a crucial adoption for manufacturing organizations that have invested in monolithic systems but are now faced with a marketplace that demands more agility and adaptability than those systems can provide. Building a layer of composable processes on top of a core system allows manufacturers to maximize the investment they made in their core system without freezing their ability to respond to a changing marketplace.
By adopting composability, organizations open the door to creating an:
- Ownership mindset that encourages domain experts to act in service of organizational goals
- IT backbone that equips domain experts to contribute to the design of simple and adaptable building blocks for a wide range of business processes
- Enterprise-wide engagement where process owners of any skill can develop tools tailored to their unique needs
The most important lesson
A low-code enterprise development platform is the perfect tool for building composable applications. Low-code applications are modular, easily shared across an organization, and constructed with an intuitive interface simple enough for non-professional developers to create apps perfectly tailored to their tasks. They open up the opportunity to include and extend legacy and in-house systems while still keeping your core clean. Low-code applications also help bridge communications between IT and business personas and stimulate the creation of fusion teams.
The sizeable Mendix library of templates and connectors means that organizations can jumpstart their transformation into a composable enterprise and create their own building blocks. And that’s one lesson that manufacturers don’t have to be taught: getting a step on the competition is always a good thing.
Watch How Automotive Supplier Schaeffler Group Democratizes App Development with a Low-Code Platform