Improving Supply Chain Collaboration with CNH Industrial

CNH Industrial is a leading global capital goods company with a strong presence in both on and off-highway applications.
It assists in:
- Providing farmers with cutting-edge technologies to help them feed a growing world population
- Building and rebuilding cities and infrastructures
- Delivering sustainable transport solutions for goods and communities, all with future-proof powertrain solutions
Its agricultural and construction equipment, trucks, commercial vehicles, buses and specialty vehicles are present in all major markets worldwide. Globally, the company has some 63,000 employees, who work across sixty-seven plants and fifty-six R&D centers.
Building these products requires the use of multiple Information Technology (IT) and Operational Technology (OT) systems that document bills of materials and their visualizations. Represented in both 2D and 3D, these visualizations describe the design and construction of a configured machine or a single piece of the equipment.
The data gathering process across these systems, which makes it possible to collaborate on parts and assemblies with engineering, purchasing, and supply chain, is often complex and time-consuming.
Facilitated by the Mendix low-code development platform, CNH Industrial built a web application called Digital Product Data (DPD) that ties together data from:
- A multi-site Teamcenter Product Lifecycle Management (PLM) implementation
- An enterprise Engineering Bill of Material (BoM) system
- A legacy drawing document management repository
With the help of Mendix, CNH Industrial’s engineers are now able to pull information from a single source to construct a model-based package for collaboration with other parts of the organization. This way, actors across the organization can understand this critical data without wasting time or resources. The application resulted in an increase in positive end-user feedback, an 85 percent reduction in system “clicks” performed by CNH Industrial employees, and a 50 percent reduction in effort previously spent using multiple systems to understand the nature of a component.
Barriers to Model-based Definition
Model-based Definition, a popular concept in the industrial space, refers to the use of 3D visualizations as a richer, more detailed means of providing specifications for components, or how those components are assembled. Having made investments in 3D visualization technology, CNH Industrial seeks to make this methodology a central part of its engineering process.
Making model-based definition a central methodology across the spectrum of engineering processes is a long journey that touches many workflows and systems. There are several engineering and business-critical systems in place today that typical engineering workflows span. For example, in order to collaborate effectively with suppliers on an assembly, engineers need to access the engineering Bill of Materials, their 3D visuals, and 2D drawings in order to act on complete information.
“What they would have to do is to start with a query in our enterprise change management system to get the information regarding the bill of material. [For] attributes like when it was released—other parts that are impacting this particular component—they would need to go to a separate system, which is an internally developed system, to get the drawings and specifications to describe the geometry of the part.”
Lastly, he added, “Going to the 3D definition would require an end user to go to one of the Teamcenter multi-site systems.”
With the problem clearly defined, Grigas and his team got to work solving it.
Engineering Efficiency
The team ultimately settled on using the Mendix platform for the Digital Product Data (DPD) application, citing:
- Accelerated project delivery time
- Alignment with a desire to use an Agile/DevOps approach to deepen collaboration with subject matter experts
- Out-of-the-box connectors for Teamcenter and 3D Viewing of JT data to simplify integration
The application itself serves as a “single pane of glass”, presenting multiple sources of data in a single interface that is brought together in context of the requested assembly or BOM. It exposes a complex, multi-site Siemens Teamcenter implementation (integrated quickly via an off-the-shelf Teamcenter Connector in the Mendix Marketplace), and custom integrations to MatrixOne’s Engineering Central, and iView for 2D Drawings. Siemens JT Viewer is utilized for a native, intuitive process for viewing 3D data.
Ultimately, DPD enables all relevant users—not only those familiar with PLM systems—to access data easily and rapidly, a significant win for CNH Industrial, and thanks to the adoption of low-code, this new way of working was made possible in only an 11-week development project, a previously unthinkable time frame.
Rohit Tangri, co-presenter of the session and GVP of Mendix Industry Solutions, echoed Grigas’ satisfaction with the project, remarking, “This composite application, on top of multiple PLM and legacy systems was delivered very successfully for CNH Industrial. We’re delighted to have helped provide the value and rapid ROI customers have come to expect from delivering these solutions on Mendix and our Xcelerator portfolio.”
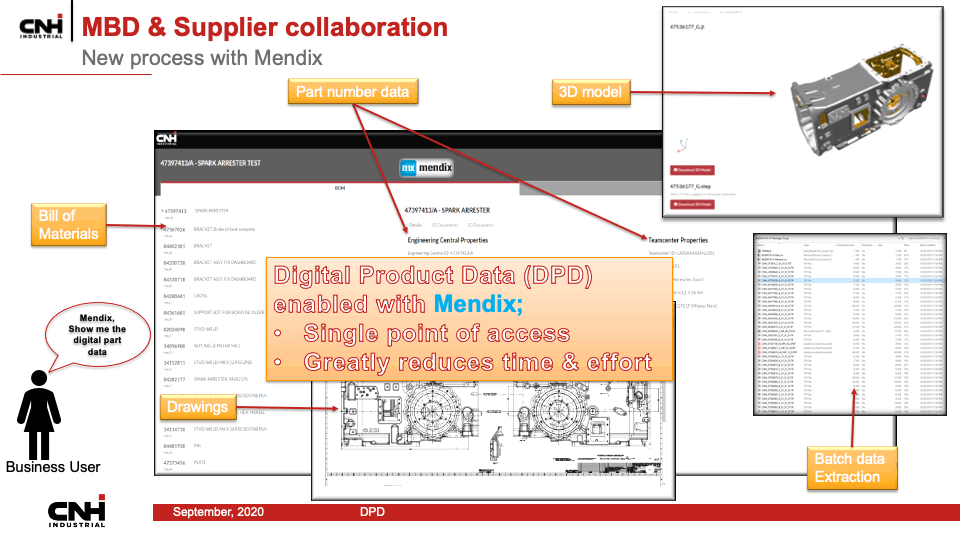
Success Defined
With information from multiple systems now transparent, simple to view, and in one location, the process of leveraging a 3D-representation of the components in an assembly is far simpler. The project has been well-received, which has led to an expansion of the production pilots. DPD is a critical part of CNH Industrial’s journey to realize model-based definition and eliminating a tedious bottleneck that required navigating to multiple legacy systems and needless, excessive keystrokes.
“Today, the drawing is a one-stop shop of information for the supply chain on how to design or manufacture that component,” Grigas concluded.